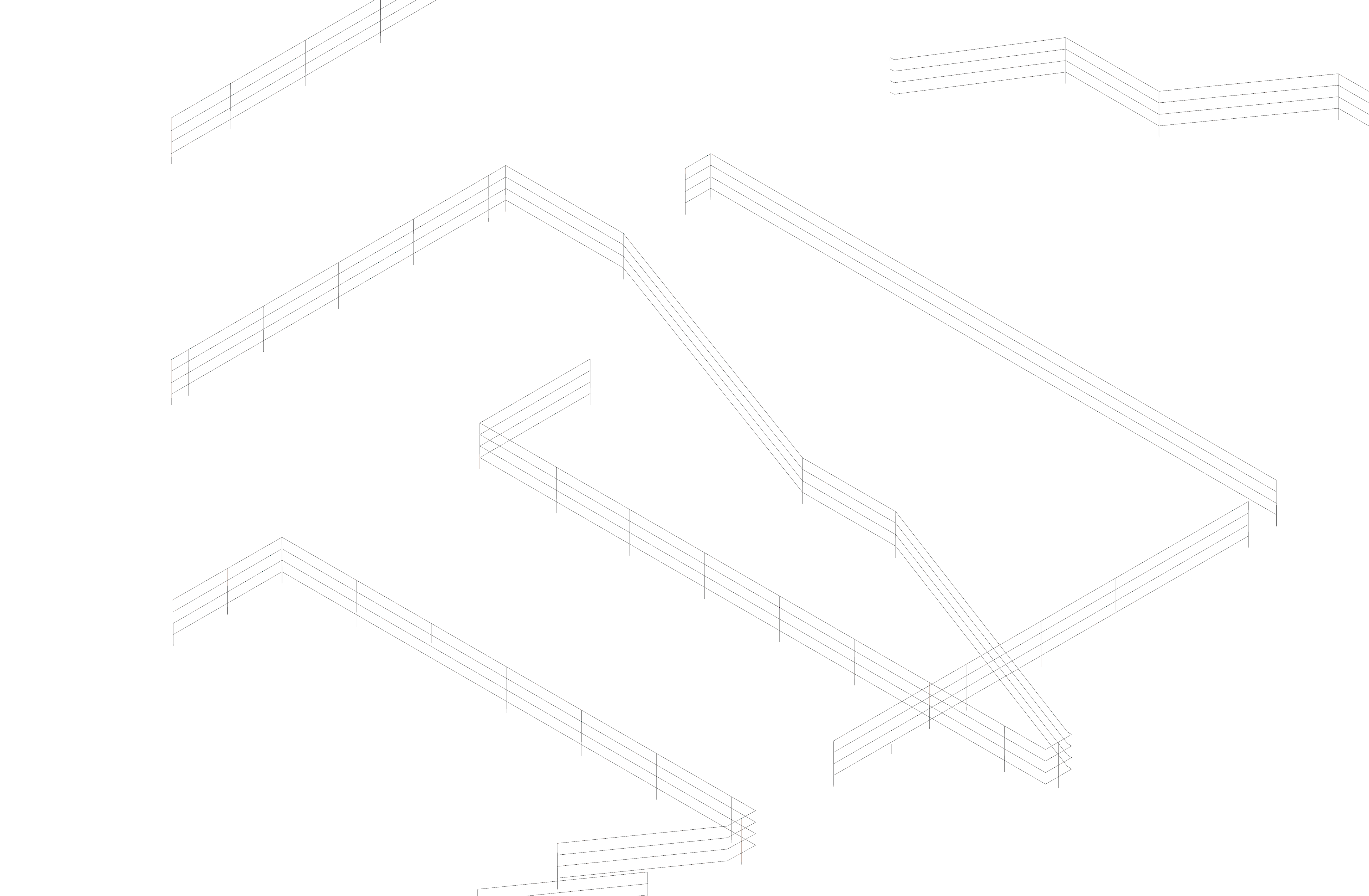
Course | M. Arch. Fall 2022 Studio
Professor | Marshall Prado
Team | Caitlin Turner, Renee Smith, Sophia Walters
Location | Art and Architecture Building, Knoxville, TN
Fiber craft and computational tools can be utilized to create interesting variations on existing architectural typologies. The ability to test a form digitally then test the stretch of a material right then and immediately apply that to the digital tool is not something you can do with every architectural process. There are still many opportunities to be explored further including side-to-side component connections, embedded materials, joint connections, and surface enclosures. That being said, the final demonstrator of this research studio is successful in showing the capabilities of looping and leaves room for many opportunities to be explored further.
Throughout this research studio, various computational tools were developed and utilized to create iterative processes and fine tune control over anchor points, end shapes, and nodes within the fiber craft form. The goal for the final form was to develop something cathedral-like that created space over the second-story bridge but also responded to the design and circulation of the architecture building. Specific anchor points were utilized in response to difficulties found in the phase three prototype and crochet ribbing was applied to provide more control over the final component form.
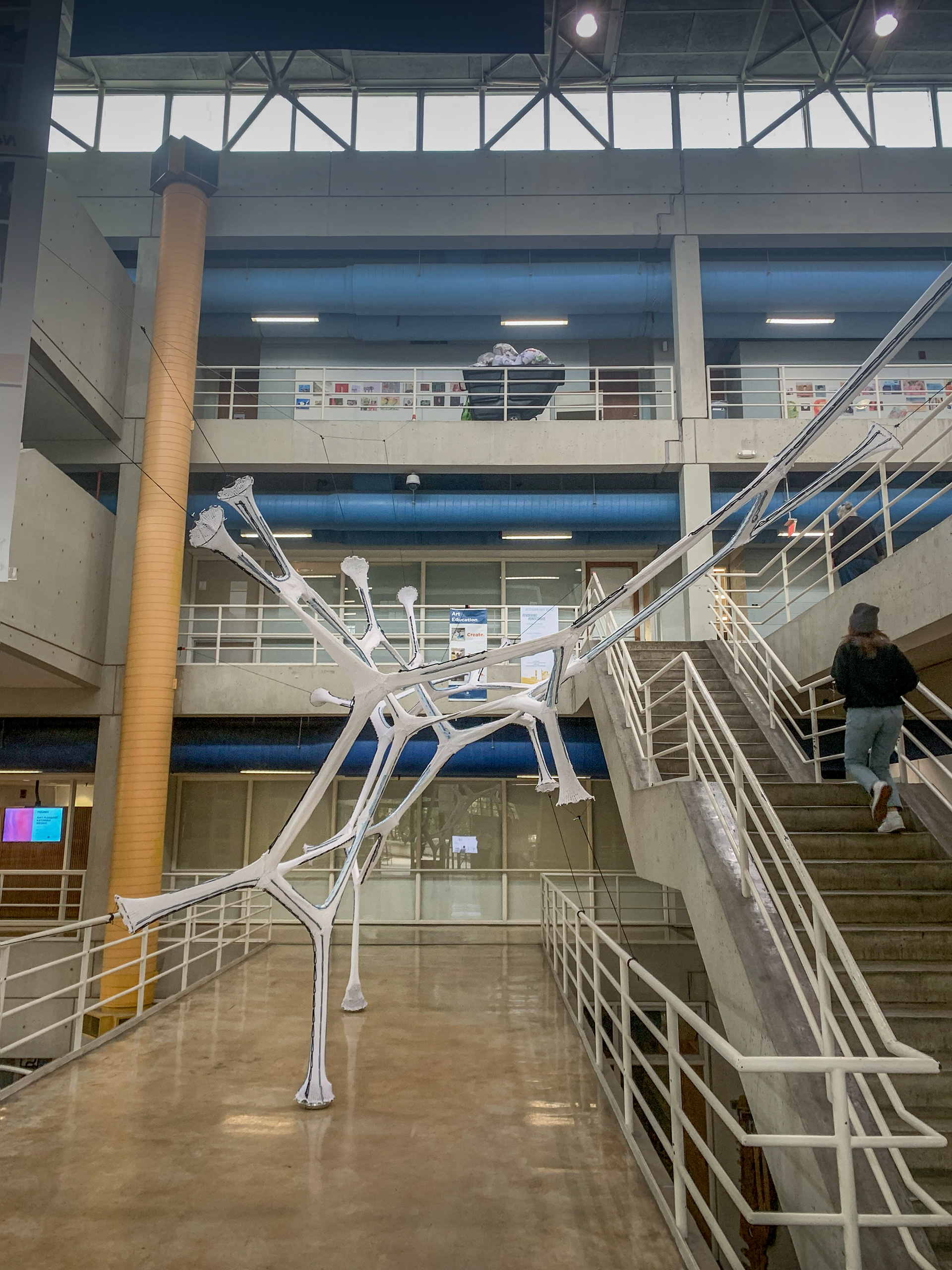
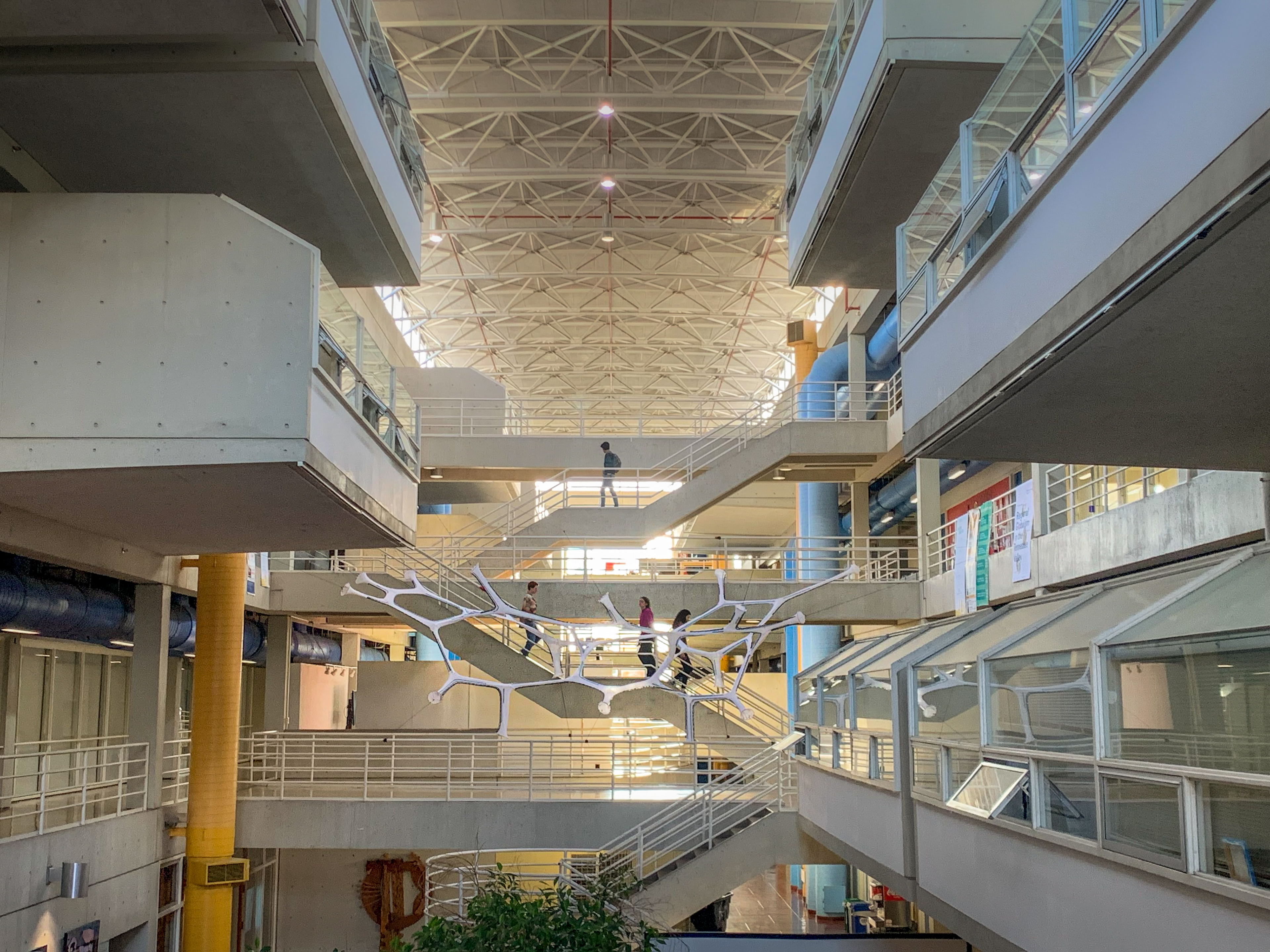
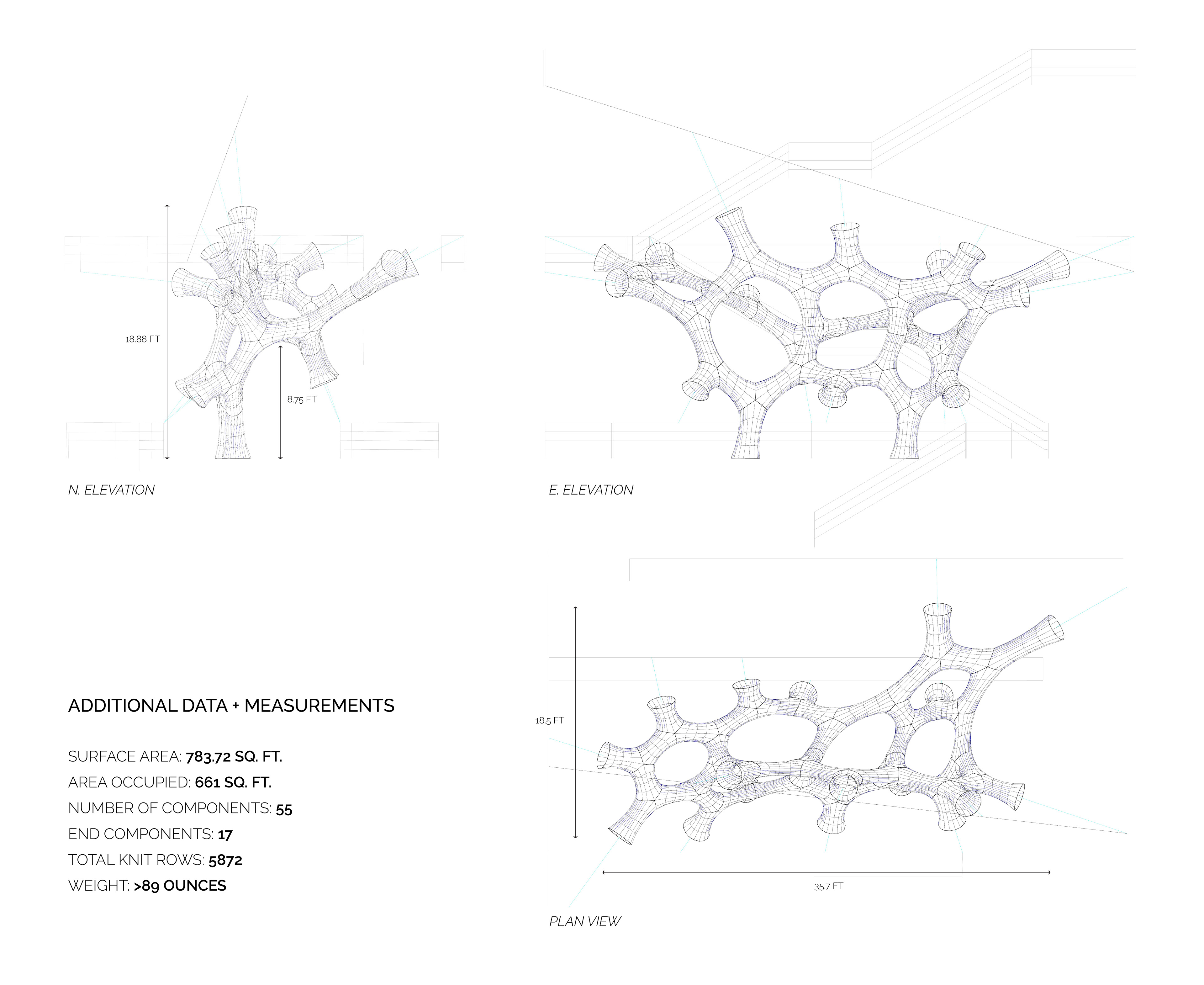
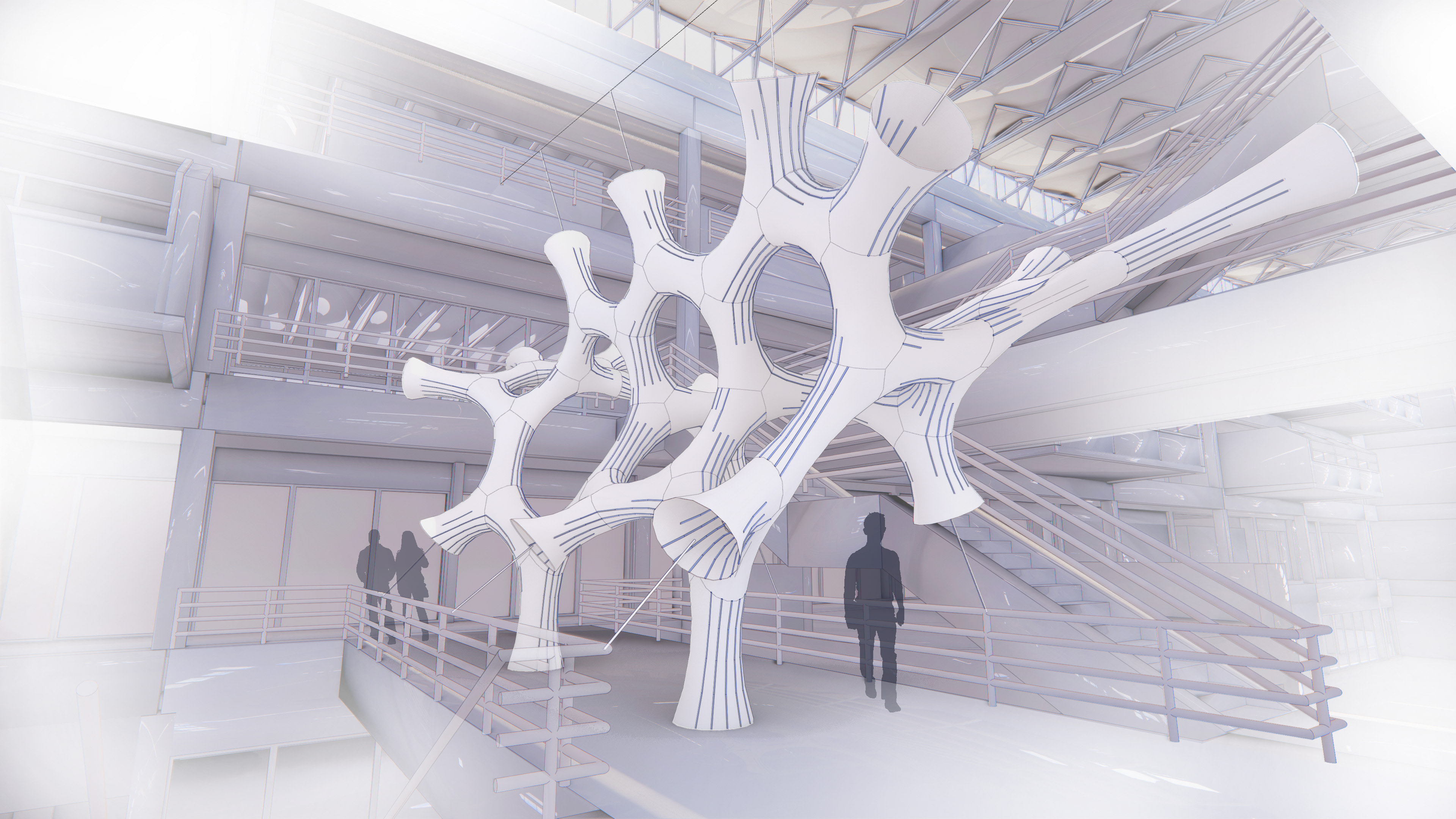
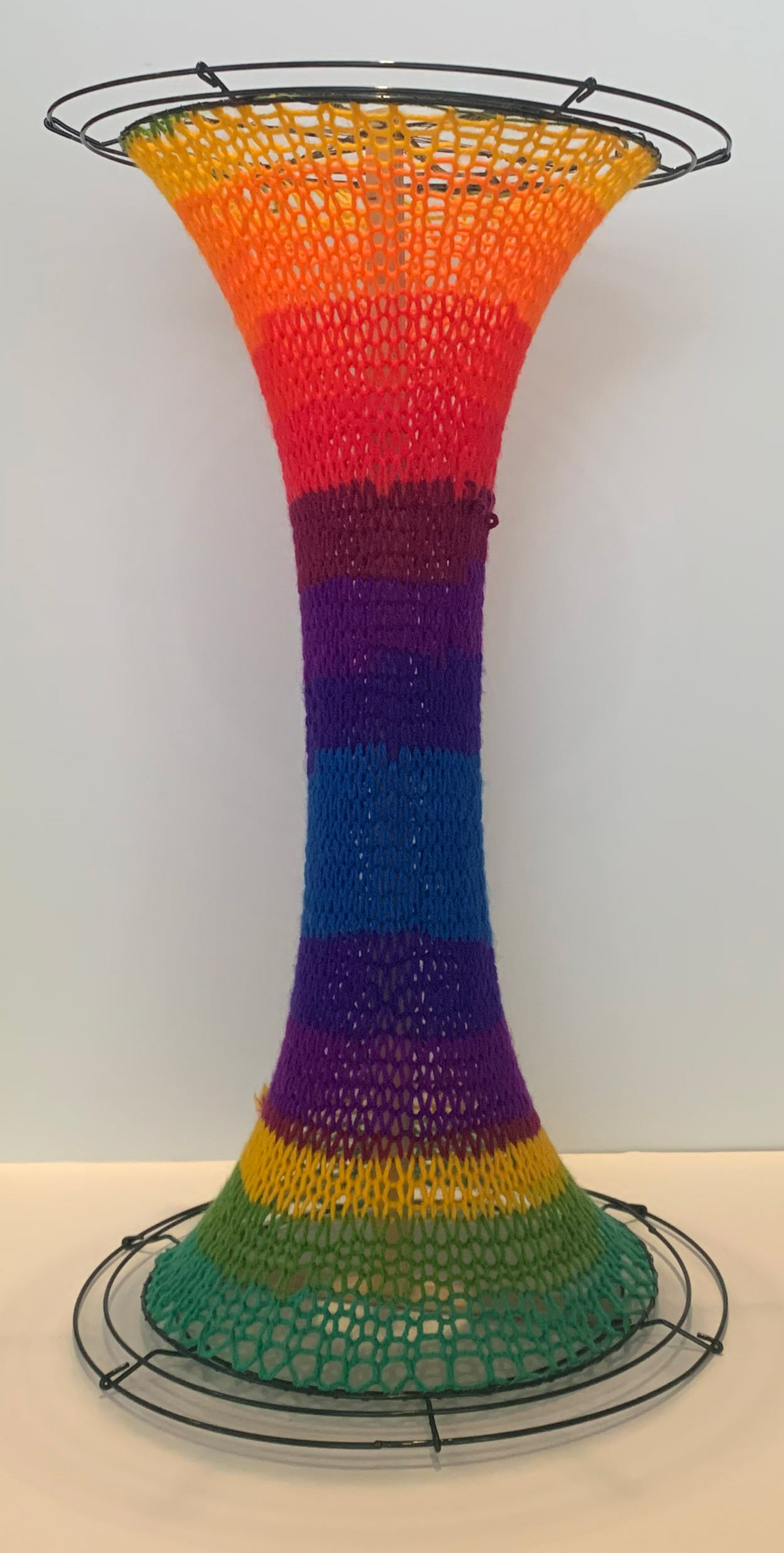
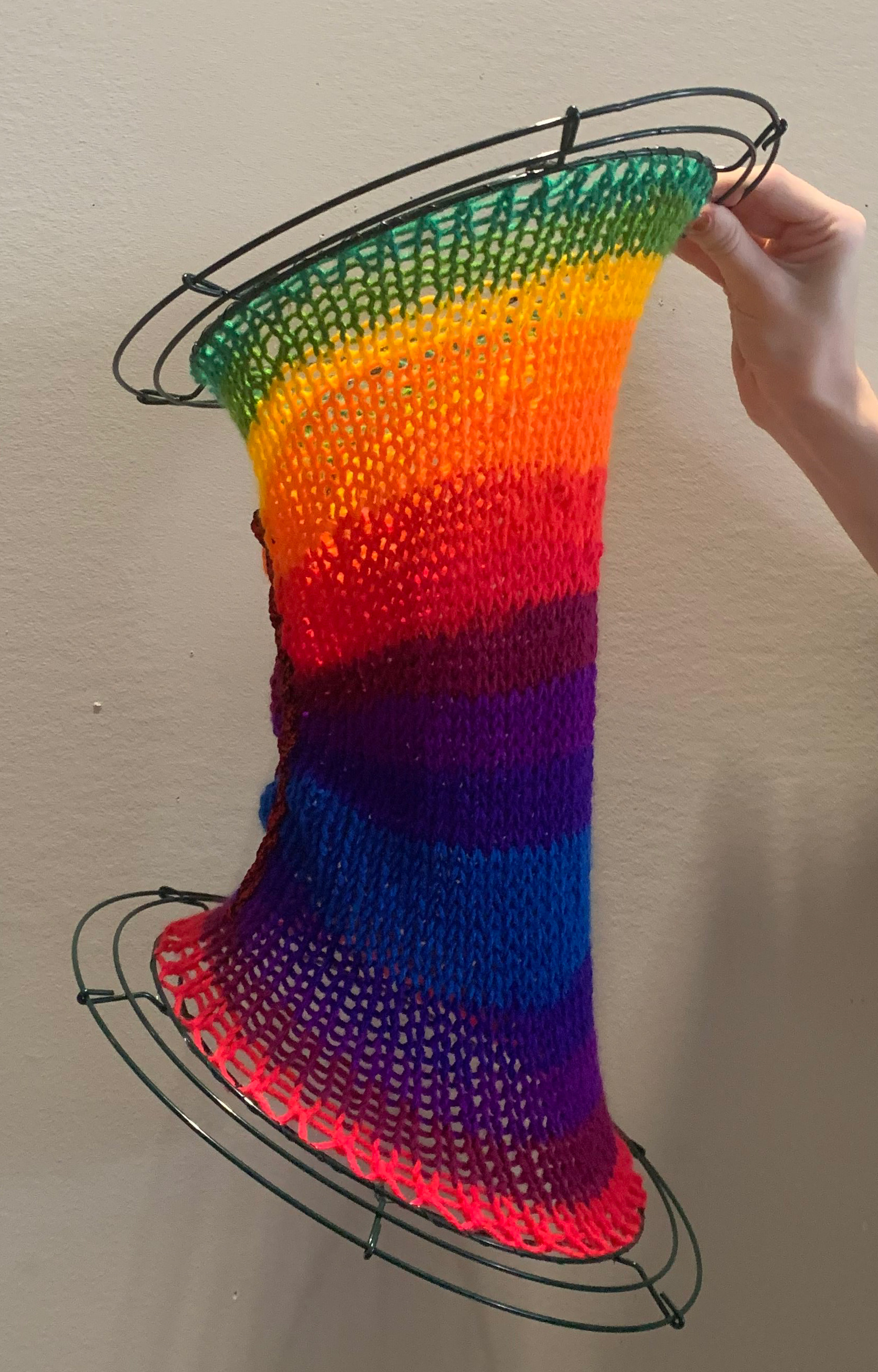
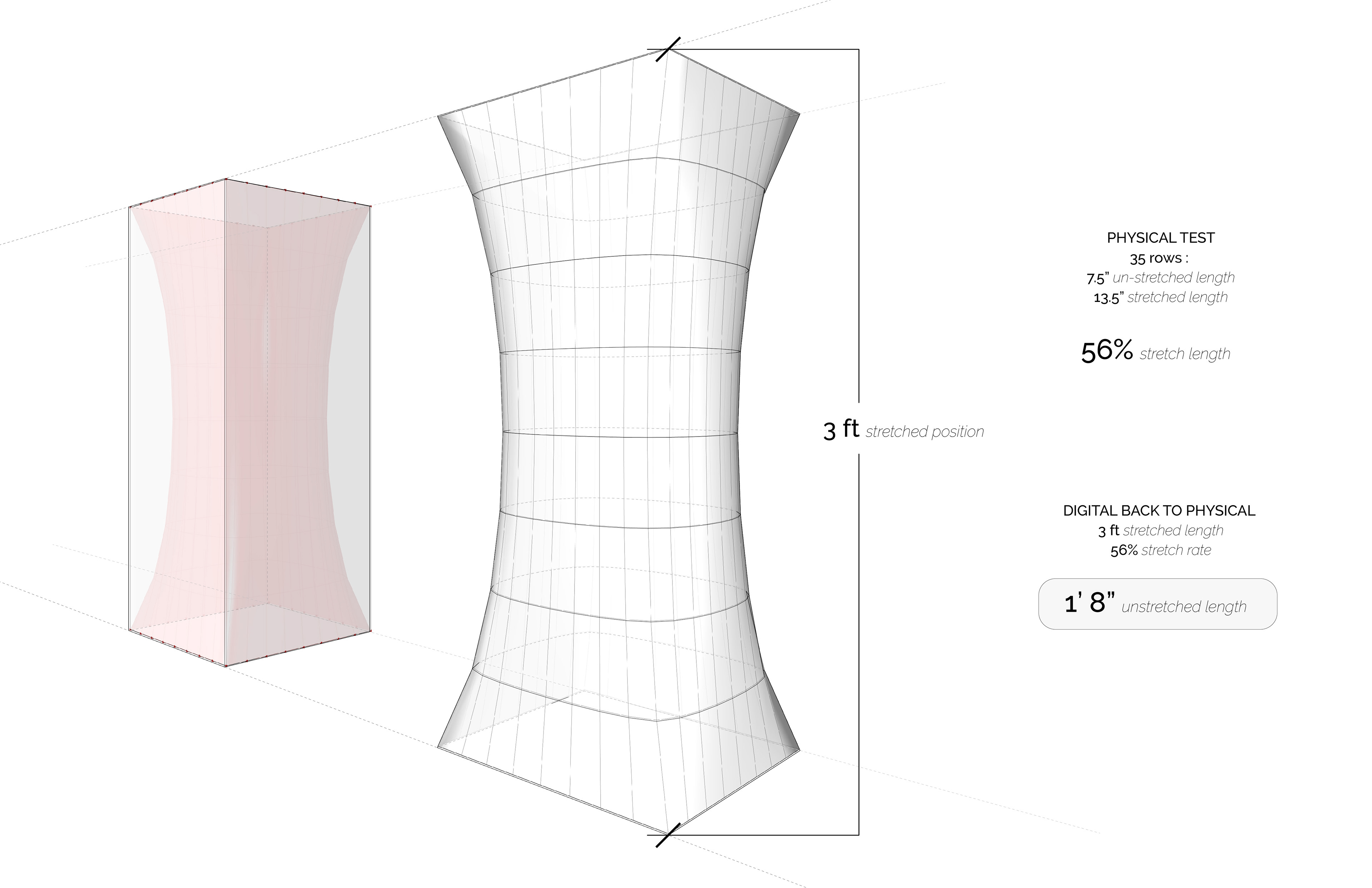
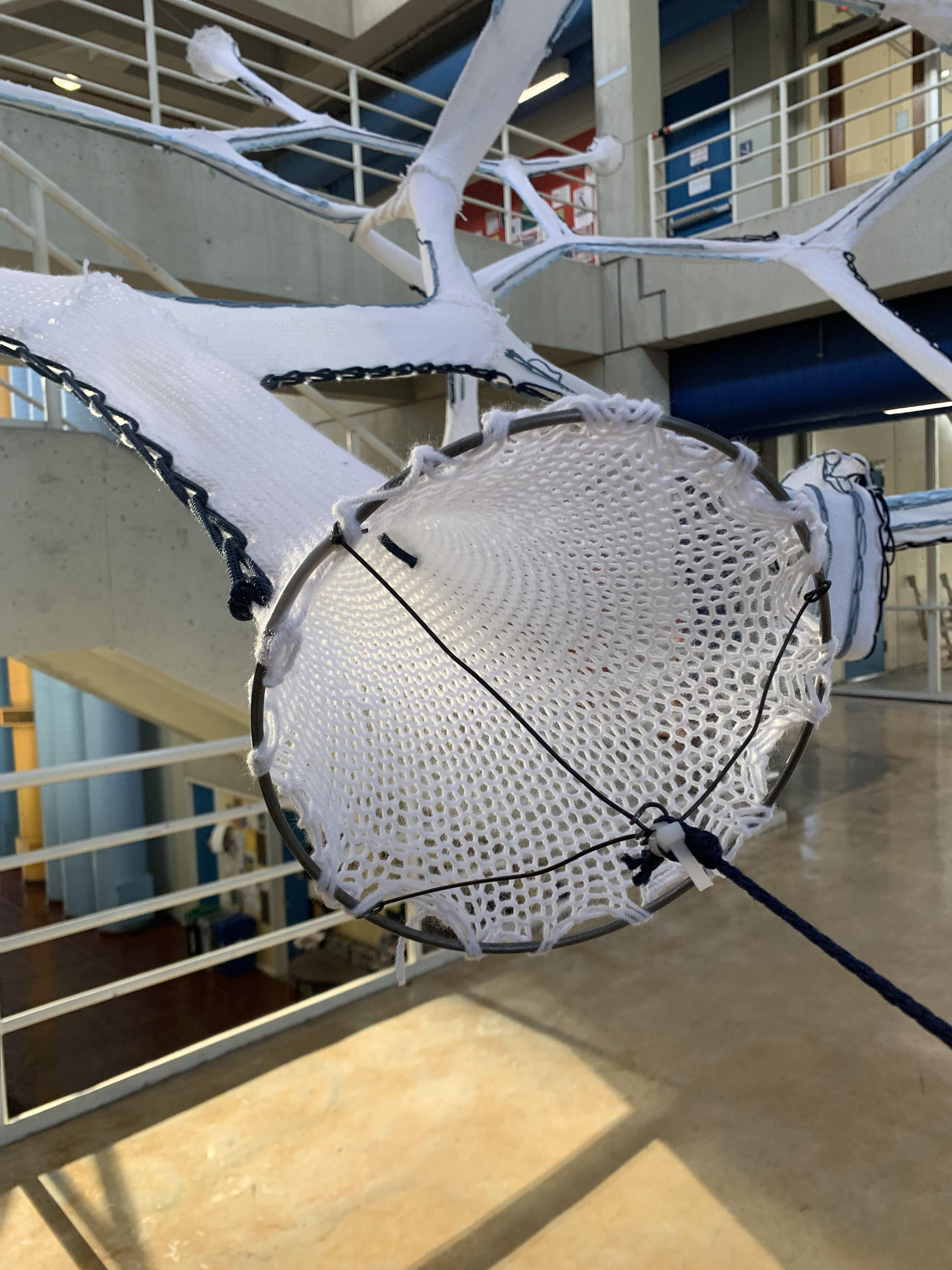
Digital Tools Process
The digital process began as a “y” component, which easily translated into a lattice system, and that larger system could then be manipulated to develop various forms. Initially meshes were plugged into grasshopper to simulate how these forms would look when pulled into tension. This allowed for the analysis of what areas would be flattened or distorted in undesirable ways; furthermore, creating an iterative process to establish ways to develop more desirable forms.
The prototype attempted to establish more of a canopy like form, test various connections, and utilize a side-to-side connection at the base to emphasize the column like form. After this form was developed, a process of moving from digital back to physical was addressed. Calculations from the physical stretch test were applied to reverse calculate necessary lengths of each component developed digitally.
The digital process began as a “y” component, which easily translated into a lattice system, and that larger system could then be manipulated to develop various forms. Initially meshes were plugged into grasshopper to simulate how these forms would look when pulled into tension. This allowed for the analysis of what areas would be flattened or distorted in undesirable ways; furthermore, creating an iterative process to establish ways to develop more desirable forms.
The prototype attempted to establish more of a canopy like form, test various connections, and utilize a side-to-side connection at the base to emphasize the column like form. After this form was developed, a process of moving from digital back to physical was addressed. Calculations from the physical stretch test were applied to reverse calculate necessary lengths of each component developed digitally.
Prototype
The fabrication and installation of this prototype allowed for a crucial understanding in what was and was not translating well from digital to physical. Lessons learned that carried into the next phase include: noting specific anchor points digitally is crucial to proper physical installation; fabrication of four-way joints is much more difficult to control; crochet ribbing could be utilized more to strengthen the form of components when pulled into tension.
The fabrication and installation of this prototype allowed for a crucial understanding in what was and was not translating well from digital to physical. Lessons learned that carried into the next phase include: noting specific anchor points digitally is crucial to proper physical installation; fabrication of four-way joints is much more difficult to control; crochet ribbing could be utilized more to strengthen the form of components when pulled into tension.
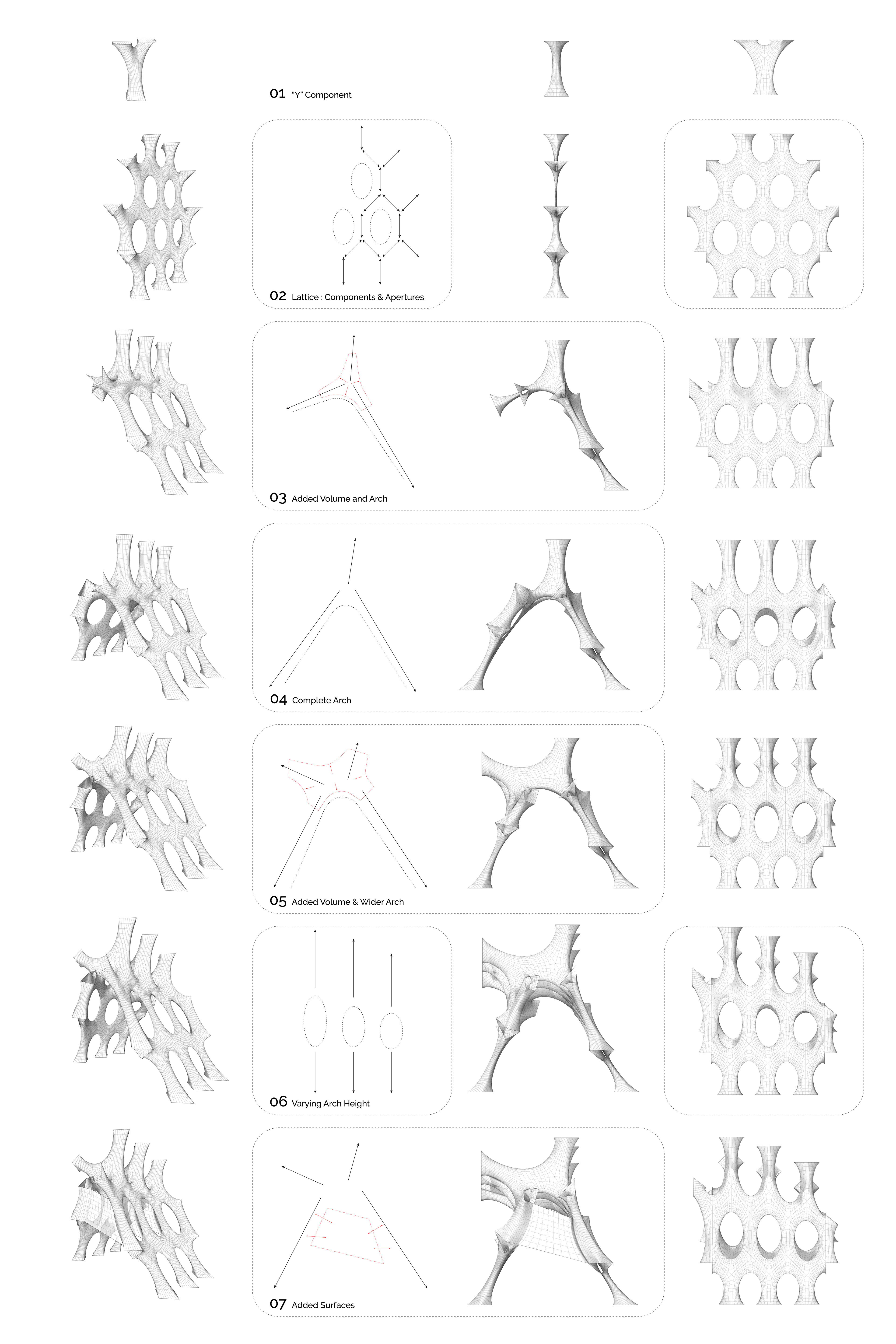
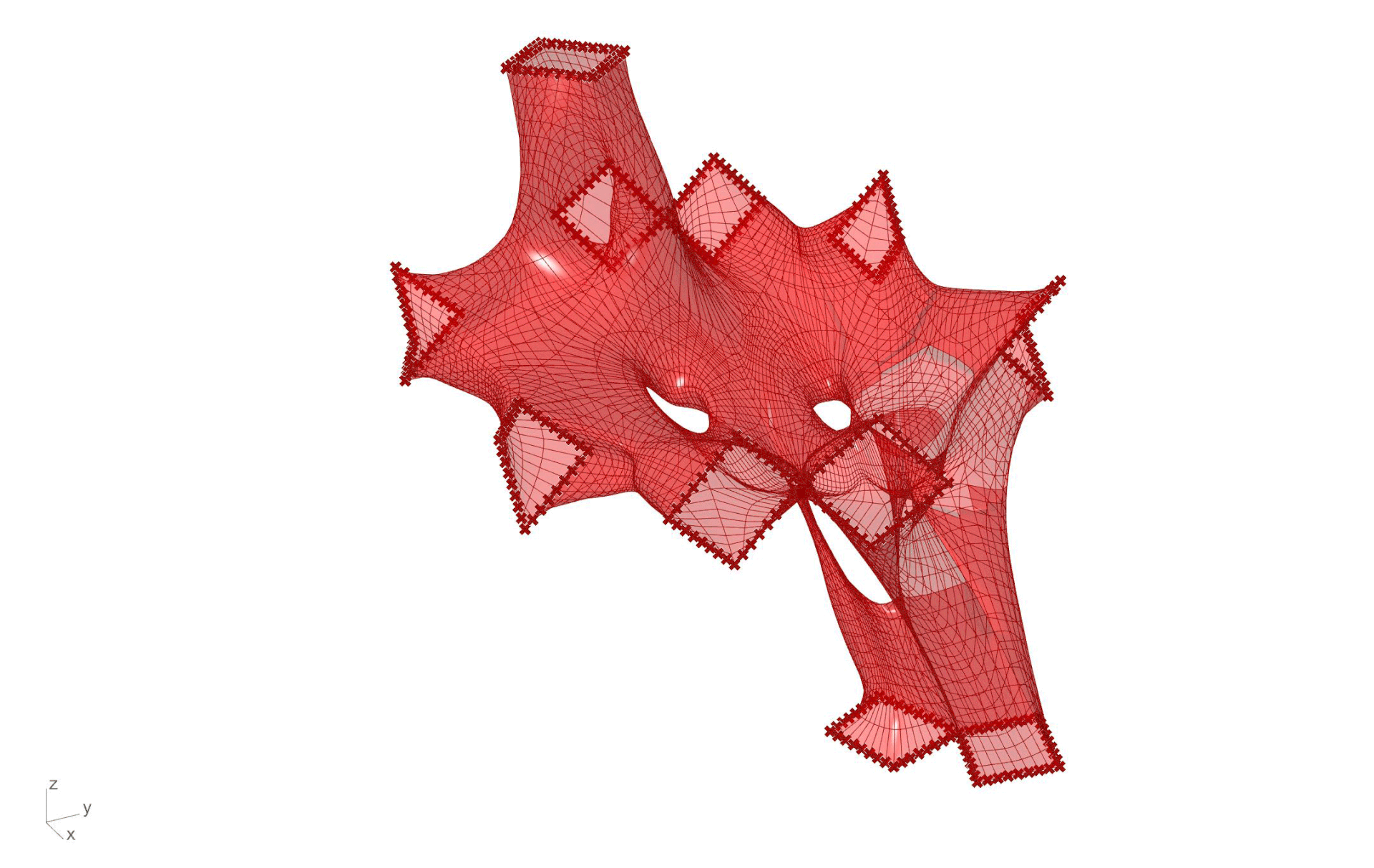
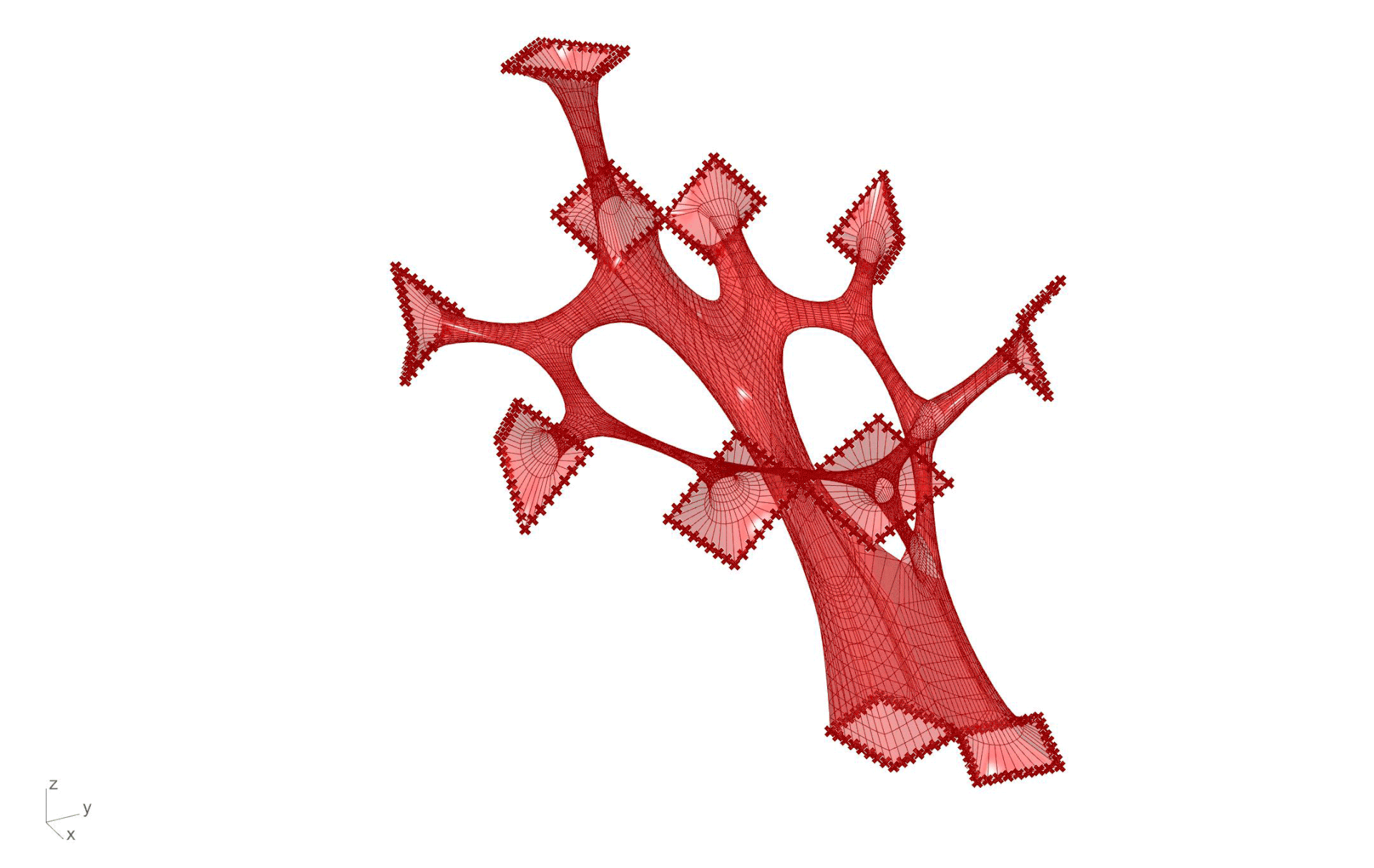
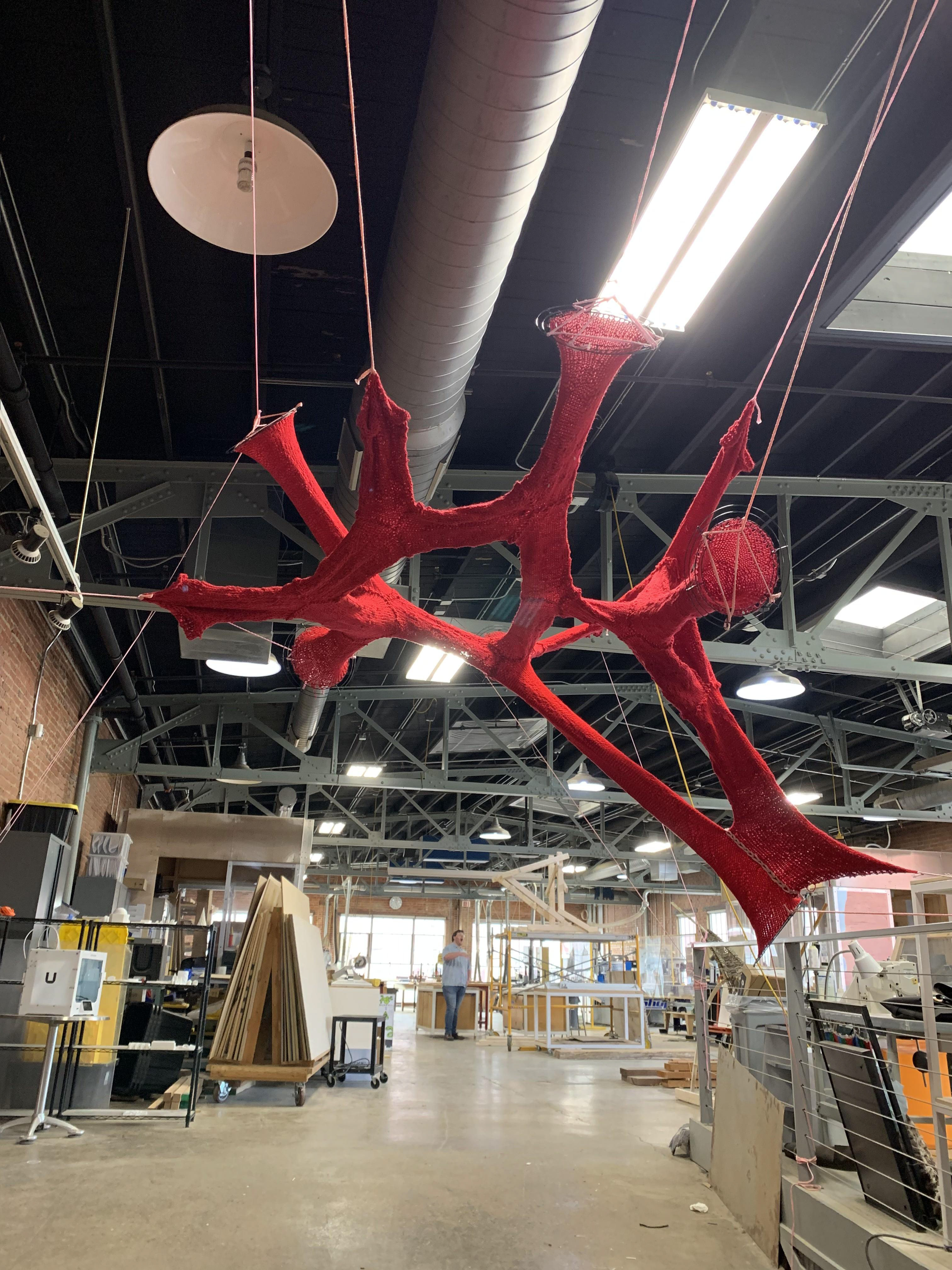
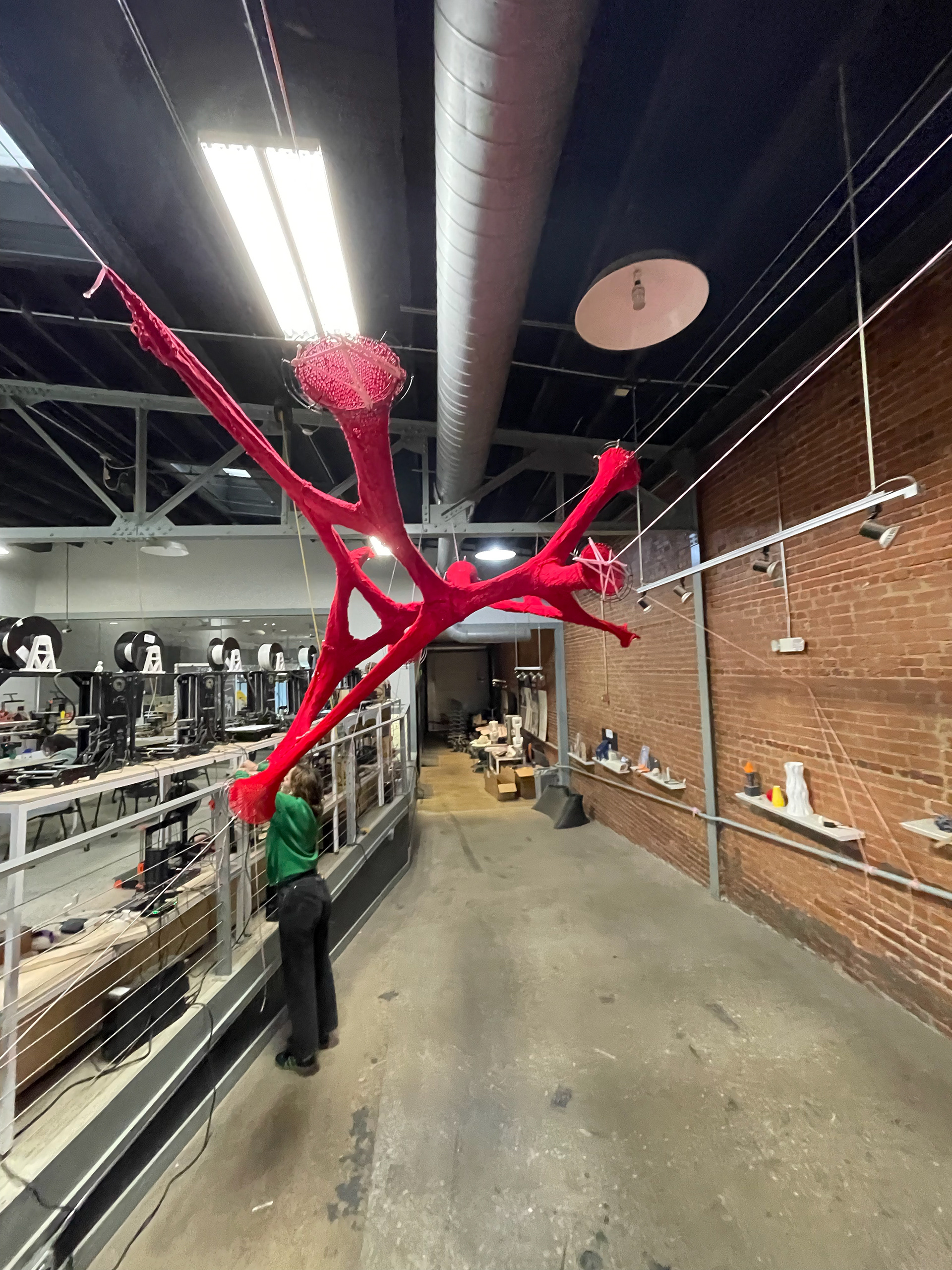